Пять шагов к более энергоэффективным чиллерам
Чиллеры являются значительным капиталовложением и главным потребителем эксплуатационных затрат как в государственных, так и в коммерческих организациях. Для многих организаций, чиллер самый большой единичный потребитель электроэнергии и он требует постоянного обслуживания для обеспечения их надежной и эффективной эксплуатации.
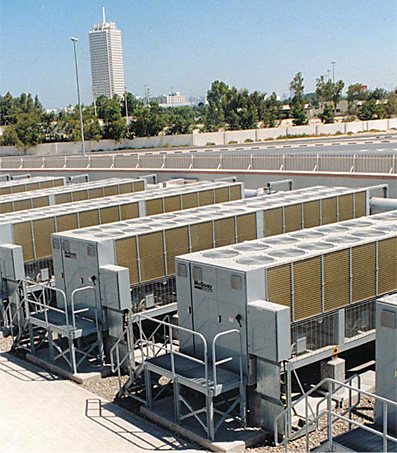
На постсоветском пространстве лишь немногие компании, в отличие от западных коллег, используют прогнозирование в техническом обслуживании - анализ вибраций, инфракрасную термографию, тест давления, создаваемого вентиляторами - для предупреждения проблем. Общее профилактическое обслуживание является ключом для обеспечения наивысшей продуктивности и эффективности чиллера.
Эффективность чиллеров непрерывно увеличивается на протяжении последних 15 лет в элементах управления, хладагентах и дизайне оборудования. В результате, чиллеры теперь более требовательны к условиям своей работы и регулярное обслуживание и правильное содержание их является более важным, чем когда-либо.
При разработке плана профилактического обслуживания для холодильных машин, сервисным специалистам следует продумать пять основных моментов:
Шаг 1. Поддерживать ежедневный журнал событий
Специалисты, следящие за чиллерами, должны документировать производительность ежедневно и сравнивать ее с соответствующими показателями запроектированных характеристик и характеристик, полученных во время старт-апа, для обнаружения проблем или неэффективно выставленных настроек. Этот процесс позволяет собрать историю изменений, которые могут быть рассмотрены и проанализированы для определения тенденций в работе устройств и предварительного оповещения о потенциальных проблемах.
К примеру, если специалисты на протяжении месяца будут наблюдать постепенное увеличение давления конденсации, они могут провести сверку с ежедневным журналом заметить и исправить возможные причины таких изменений, такие как загрязнение конденсаторных трубок или наличие неконденсируемых частиц в системе (вода, воздух). Многие современные чиллеры управляются микропроцессором, так что сервисные специалисты могут автоматизировать процесс сбора требуемой информации.
Шаг 2. Держать трубы чистыми
Еще одним потенциальным препятствием для достижения желаемой производительности чиллера является эффективность теплопередачи. Производительность и эффективность чиллера непосредственно связаны с его способностью к передаче тепла, которая начинается с чистых трубок испарителя и конденсатора. Большие чиллеры могут насчитывать несколько километров трубок в своих теплообменниках, поэтому содержание этих поверхностей в чистоте имеет существенное значение для поддержания высокоэффективной работы.
Эффективность чиллера ухудшается по мере того как трубы загрязняются, когда грязь, водоросли, осадок, накипь или другие загрязнители накапливаются на внутренней стороне теплообменников. Уровень загрязнения зависит от типа системы (открытая или закрытая), а также качества воды и температуры.
Многие производители рекомендуют производить очистку трубок конденсатора ежегодно, если они являются частью открытой системы и раз в три года, если они являются частью закрытой системы.
Сервисные специалисты могут использовать два основных метода очистки трубок:
-
Механическая очистка для удаления грязи, водорослей, осадков и сыпучих материалов.
-
Химическая очистка для удаления накипи. Большинство производителей чиллеров рекомендует консультироваться у местных организаций, специализирующихся на очистке воды, для определения эффективных химических решений.
Обычно, новые чиллеры могут быть оснащены функцией автоматической чистки труб в системе, которая может быть интегрирована в уже существующую холодильную систему. Эти системы очистки используют небольшие щетки с нейлоновой щетиной, которые проходят через очистные трубы. Стандартный четырех ходовой реверсивный клапан устанавливается в систему трубопроводов конденсатора и каждые 6 часов на 30 секунд система автоматически меняет направление потока жидкости через конденсатор. Совместно с надлежащей очисткой воды эта система практически полностью устраняет загрязнение внутри холодильной установки и поддерживает запроектированные значение температур. Эти системы обычно окупаются за два года.
Шаг 3. Обеспечение отсутствия утечек
Многие производители рекомендуют ежеквартальную проверку фреонового контура на предмет утечки. Невозможно создать полностью герметичную систему и утечки неизбежно приведут к присутствию воздуха и влаги (так называемых неконденсирующихся частиц).
С того момента, как неконденсирующиеся частицы попадают в конденсатор, возрастает давление конденсации и требования к мощности компрессора, снижается эффективность и общая мощность охлаждения.
Наличие влаги в чиллере может привести к возникновению кислот и коррозии в обмотке и подшипниках компрессора, а также ржавлению корпуса. Небольшие частички ржавчины, под названием штрафы, плавают в системе и застревают внутри труб теплообменника. Штрафы в трубках снижают эффективность передачи тепла и общую эффективность в работе чиллера. Оставленные без внимания, они могут привести к дорогостоящему ремонту труб.
Утечки также приводят к низкому содержанию хладагента и другим эксплуатационным проблемам, таким как снижение давления испарения, что приводит к перегрузке компрессора. Для чиллеров работающих на высоком давлении, специалисты должны отслеживать уровень хладагента и давление испарения для обнаружения утечек.
Шаг 4. Надлежащая очистка воды
Большинство чиллеров используют воду как хладоноситель, поэтому вода должна быть должным образом подготовлена во избежание образования накипи, коррозии и биологических веществ. Для закрытых водяных систем, частью которых чаще всего является испаритель чиллера, достаточно одноразовой химической обработки.
Открытые водные системы обычно используются в связке с конденсатором. Использование таких источников как градирни требует постоянной химической обработки. Так как в нашей стране вопрос о качестве воды стоит очень остро, то сервисным специалистам необходимо в обязательном порядке уделить внимание водоподготовке.
Кроме того, желательно проводить очистку всех фильтров не реже чем раз в три месяца. Стандартные фильтры достаточно эффективно очищают воду, если за ними следить должным образом. Чтобы определить, когда пришло время очистки, необходимо следить за перепадом давления на фильтре и выполнять рекомендации производителя по их очистке.
Обслуживание фильтров ограничивает эрозию трубок теплообменника, которая возникает из-за песка или других мелких частиц, движущихся на высоких скоростях. Эрозия и крошение труб снижает эффективность передачи тепла и общую эффективность. Если не исправить ситуацию, то это может привести к закупориванию труб и общему отказу системы.
Специалисты должны ежегодно проверять жидкость в системе на наличие коррозии и эрозии. Большинство производителей рекомендуют вихретоковый контроль теплообменников, включая электромагнитную процедуру определения толщины стенки, каждые три-пять лет.
Шаг 5. Анализ масла и хадагента
Ежегодный химический анализ масла и хладагента может помочь обнаружить загрязнения, прежде чем они станут серьезной проблемой. Тестирование состоит из спектометрического химического анализа для определения загрязнителей, таких как влага, кислоты и металлы, препятствующие производительности и эффективности в работе чиллера.
Изымать образец масла следует на работающем оборудовании. Заменять масло необходимо по показаниям химического анализа. Специалисты также должны обследовать масляные фильтры на предмет падения давления и менять их, если оно выходит за допустимые пределы, а также при каждой замене масла.
Анализ масла также может помочь обнаружить и другие проблемы в чиллере. Например, высокое содержание влаги может сигнализировать о проблемах с группой очистки, а изменение некоторых характеристик масла может говорить о развитии неприемлемого износа компрессора.
Специалисты используют тестирование хладагентов для обнаружения загрязнителей, которые могут привести к снижению надежности и эффективности. Одним из основных загрязнителей является масло, которое попадает в хладагент. Производители чиллеров подсчитали, что каждый 1% масла в хладагенте дает снижение производительности на 2%. И это не редкость обнаружить в старых хладагентах до 10% масла. Исходя из этой оценки, такое загрязнение может привести к 20% снижению производительности. Итог - своевременное тестирование может избавить от больших затрат.
Правила использования материалов сайта
|